Passive Fire Protection
Passive Fire Protection
Norimax Passive Fire Protection Team specializes in application of intumescent fireproofing coatings for hydrocarbon-fires and jet-fires in the Oil & Gas environment. Norimax PFP applies both solvent-based and water-based intumescent fireproofing coatings.
Norimax PFP team also specializes in the installation of fire-jackets for valves and actuators.
The Effect of Fire on Intumescent Coating
Intumescent fireproofing coating swells to >40 times in volume when burnt by fire.
The swelling is due to exothermic reaction of the fire-resistant chemicals in the coating.
The swelling insulates the steel below the coating while swelled coating maintains its integrity for up to 2 hours.
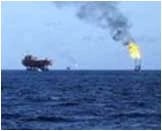
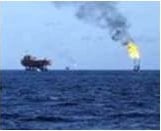
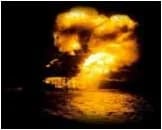
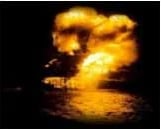
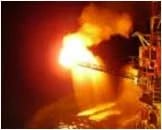
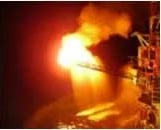
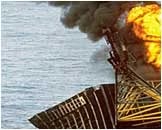
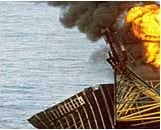
PFP Application
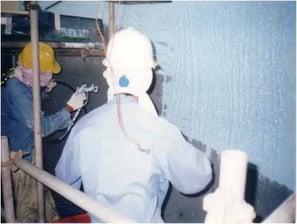
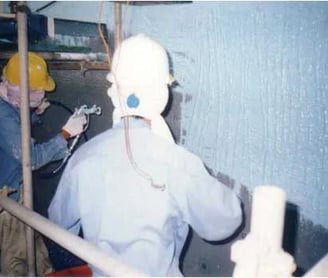
Fireproofing
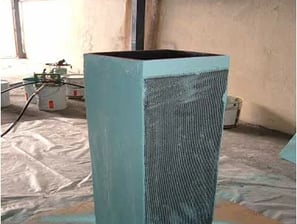
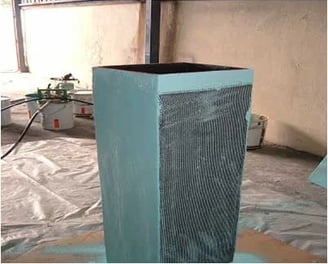
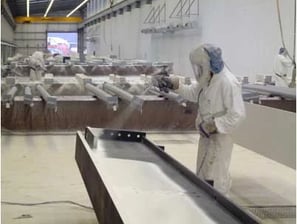
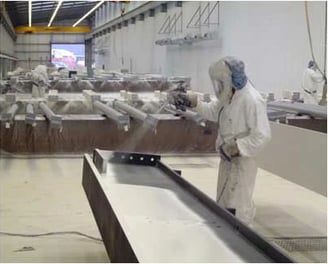
Maintain Structural Integrity of Metal Supports before collapse. Steel structure collapse within 5 minutes in hydrocarbon fire.
Norimax is approved applicator for
ALBI –water-base
PITT-CHAR – solvent-base
Active Fire Protection
Require mechanical trigger to activate the system.
To extinguish the fire.
Sprinklers
Fire Extinguisher
Hose Reel
Passive Fire Protection
Fireproofing systems such as coatings, jackets & blankets which do not need mechanical activation.
To protect structures under fire.
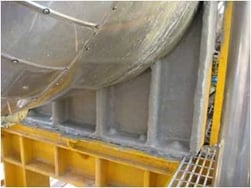
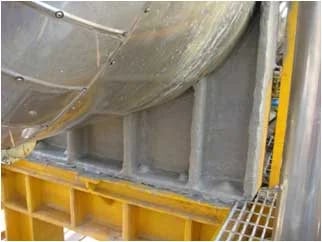
Passive Fire Protection Materials
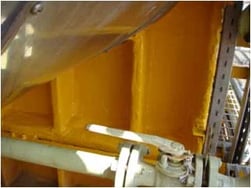
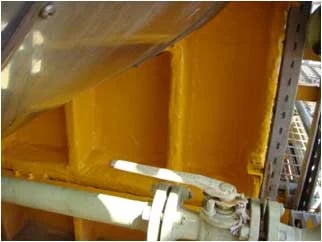
Concrete
Cementitious Products
Epoxy Intumescent Coatings
Acrylic Intumescent Coatings
Fire Proofing Casting
Fire Proofing Jackets
Concrete
Example: 6 inches for 2 hours fire protection
Concrete spalls after 2 hours and fire penetrate to the steel column
Cementitious
Example: Mandoval, Pyrok, Pyrocrete
Made from volcano ash (Vermiculite), mineral fiber, etc.
2-3 inches for 2 hours fire protection Spalls after 2 hours and fire penetrate to the steel column
Intumescent Coating
Firetex M90 – solvent based
Chartek 7 - solvent based
Pittchar - solvent based
Thermolag - solvent based
ALBI 800 – water based
5-20mm thickness for 2 hours fire protection
Passive Fire Protection Intumescent Materials
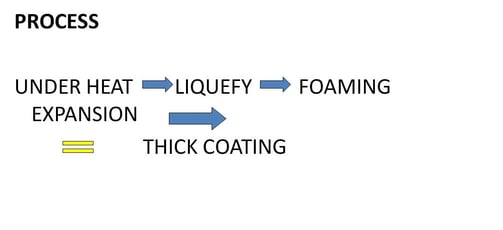
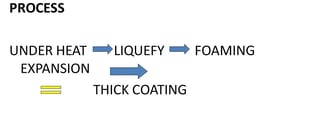
Passive Fire Protection Standards/ Fire Rating
Cellulosic < 1000º C Hydrocarbon Fire > 1000 º C
Cellulosic-timber, fabric, paper, etc. Hydrocarbon-chemicals, fuels, gas, petroleum
Jet Fire- hydrocarbon fire from fractured riser pipe or product pipeline, etc.
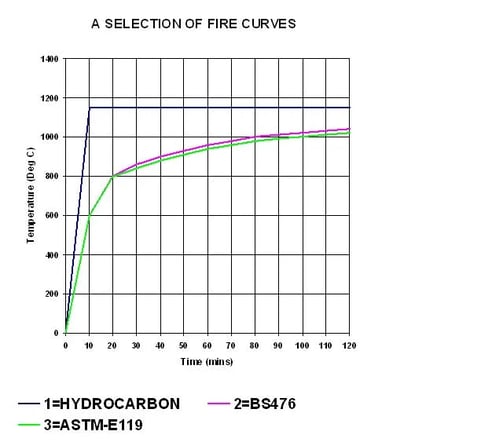
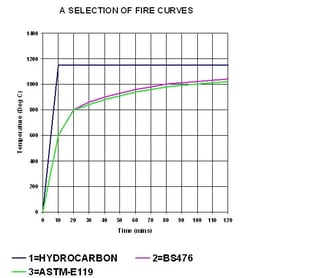
Steel start to buckle & collapse at about 550 deg C
Test Standards of Passive Fire Protection
(Cellulosic)
BS 476 Part 7-Fire tests on building materials and structures
ASTM E119-Fire tests of Building Construction and Materials
ISO 834-Fire-resistance tests-Elements of building construction
Test Standards of Passive Fire Protection
(Hydrocarbon)
UL 1709 Rapid Rise Fire Tests of Protection Materials for Structural Steel
Jet fire-Sintef Test (Norway)
Jet fire-British Gas Test (Spade Adams-UK)
Testing Bodies
Underwriter Laboratories (UL)-USA
Norwegian Petroleum Directorate (NPD)
Sintef (Norway)
Det Norske Veritas (DNV) - Norway
Lloyds Register - UK
BAM - Germany (vessels)
ExxonMobil - US
Fire Test Heat Flux
Cellulosic Fire 100kW/m²
Hydrocarbon Fire 200kW/m²
Jet Fire 300kW/m²
TEST CRITERIA
STABILITY - The construction must remain stable during the period of the fire and must not collapse.
INTEGRITY - The construction must maintain its integrity during the test period such that no gaps of sufficient width open up to allow penetration of flames.
INSULATION - The fire insulation properties of the construction must be such that unexposed face must not increase in temperature by more than an average of 140°C or by more than 180°C at any one point for the duration of the test i.e 2 hours.
Passive Fire Protection Ratings
Structural Integrity (Load Bearing)
"A" rating (Cellulosic) = 60 minutes.
"H" rating (Hydrocarbon) = 120 minutes.Non-load bearing
"B" rating from 15 minutes .Insulation
"A0" (Cellulosic) = 60 minutes Fire Protection + No Insulation Required-No limit on back face.
"A60" (Cellulosic) = 60 minutes Fire Protection + 60 minutes Insulation-Back face limit required.
"H0" (Hydrocarbon) = 120 minutes Fire Protection + No Insulation Required.
"H60" (Hydrocarbon) = 120 minutes Fire Protection + 60 minutes Insulation.
"H120" (Hydrocarbon) = 120 minutes Fire Protection + 120 minutes Insulation.
Section Factor Hp/A
Hp = Perimeter of section exposed to fire (m)
A = Cross sectional area of the steel member (m²)
Large Perimeter (Hp) will receive more heat than smaller perimeter.
Greater cross sectional area (A) of a section, the greater is the heat sink.
Hp/A = Rate at which a section will heat up in a fire he higher the value, the greater will be the protection thickness.
"Each manufacturer has their own product thickness tables based on test reports."
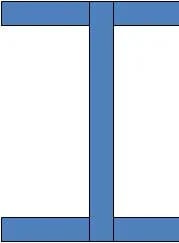
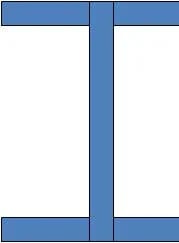
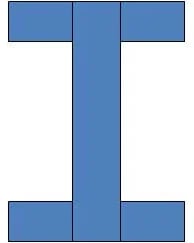
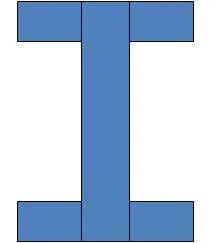
High Hp Low A Fast Heating (Requires more insulation)
Low Hp High A Slow Heating (Requires less insulation)
Passive Fire Protection Intumescent Coatings
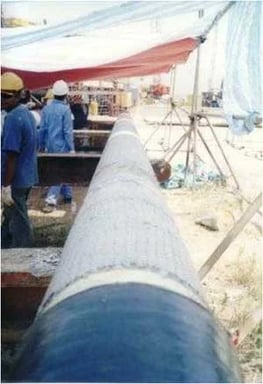
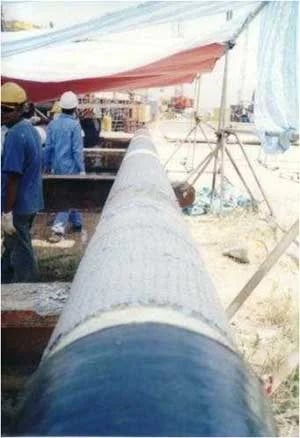
Reinforce Mesh - ensure the material stays in place during the intumescent reaction.
Types of Mesh
Chicken Wire Mesh - require pin
Carbon Mesh (Scrim) - no pin required i.e subject to site/project requirement
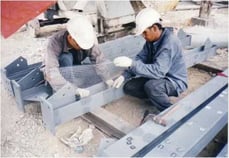
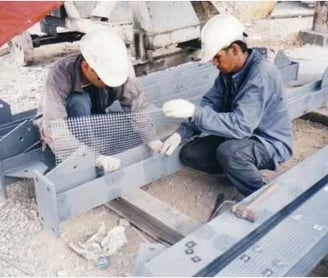
Areas That Require Mesh
Coating thickness more than 5 mm, e.g. Firewall Installation of Mesh
Pinning-mesh is installed at mid depth of the PFP thickness.
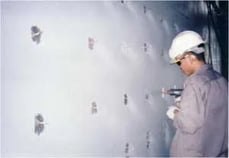
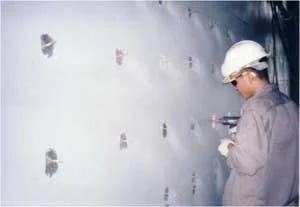
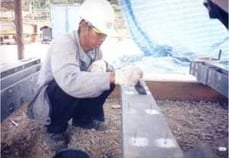
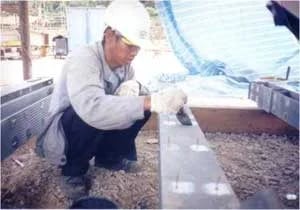

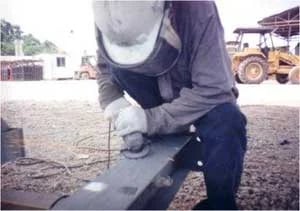
Top Coat
Color Coding
Cosmetic
Weather Resistance
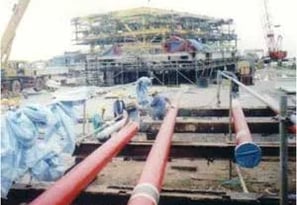
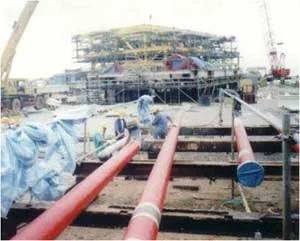
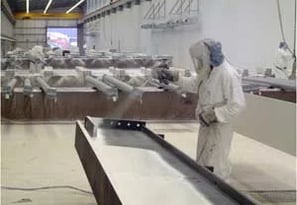
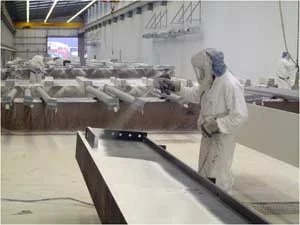
Application
Relative Humidity < 85% sensitive to high humidity
Steel Temperature < 50°C
Curing Time 2 hrs @ 23°C
Spray Pump/Roller/Trowel
Safety Precaution
Respirator
Safety Glass
Rubber Glove
Coverall
Protected Mixing Area
Quality Control
- Surface well primed and free from contamination
WFT / DFT
Mixing Ratio
Homogeneous
Thinning should not be more than 5%
No Exposed Carbon Mesh/Chicken Wire Mesh (Fully Covered with PFP Materials)
Meshing at mid depth of the total thickness
Topcoat shall be applied within 7 days of PFP curing (surface should be free from surface contaminants)
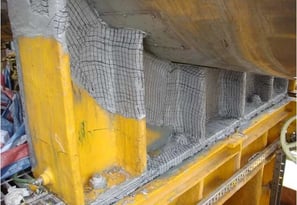
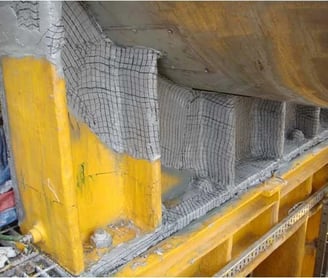